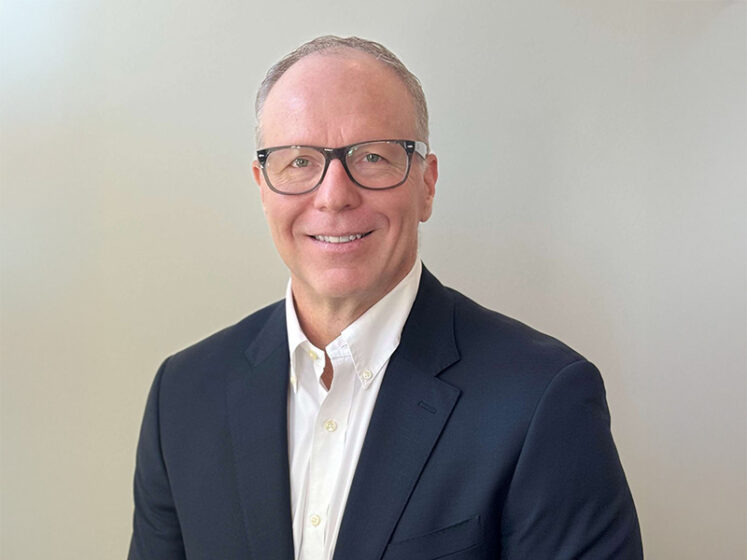
-
- Industry Solutions
-
Airport
- Airport
- Airport Industry
- Project Management
- Baggage Handling System Software and Controls
- Check-In
- Hold Baggage Screening
- Baggage Transport and Sortation Systems
- Baggage Storage and Batch Building Systems
- Make-Up and Unloading Systems
- Baggage Reclaim Systems
- Modernisation Airports
- Airport References
- Building Materials
- Cement / AFR
- Chemical Industry
- Courier, Express & Parcel (CEP)
- E-Commerce
- Minerals & Mining
- Ports & Terminals
- Power Plants
- Fashion
- Consumer Goods
- Retail
- Fertilizer Industry
- Metallurgy
Sustainability made differentOur Commitment to Sustainable DevelopmentAs an independent and family-owned company, BEUMER Group is deeply committed to the principles of sustainable development. Through strong partnerships we have developed a deep understanding of the sustainability issues of our key industries and enable our partners to achieve their sustainability goals and targets.Learn more -
- Products & Systems
-
Baggage Handling System
- Baggage Handling System
-
Airport Software Suite
- Airport Software Suite
- Business Intelligence – Learning and planning
- Flight Allocation – Being well prepared
- Handler Tools – Providing the right options
- Maintenance Tools – Providing the right means
- Routing & Sorting – Ensuring an efficient execution
- Supervision – Having the complete overview
- Software – The right partner
- Automated Container Unloader
- BEUMER autover® Independent Carrier System
- Baggage Loader
- Baggage Manipulator
- Baggage Unloader
- CrisBag® Independent Carrier System
- CrisBag® Self Bag Drop
- CrisBelt® Conveyor System
- CrisCheck® Check-In Conveyor
- CrisClaim® Baggage Carousels
- CrisStore® Dynamic Racking Solution
- Security Screening
- Tilt-Tray Loop Sortation System
-
Logistics Systems Technology
- Logistics Systems Technology
- CEP Software Suite
-
Warehouse Control System
- Warehouse Control System
- W&D – Business Intelligence – Learn and Plan Through Insights
- W&D – Maintenance and Service Tools – Have the Right Means
- W&D – Material Flow Control – Enable End-to-End Efficiency
- W&D – Order Fulfilment – Ensure Precision and Boost Efficiency
- W&D – Supervision – Have the Complete Overview
- W&D – Training – Create Skilled and Confident Personnel
- Automatic Parcel Singulator
- BEUMER Tipping Station
- BG Line Sorter
- BG Parcel Belt Conveyor
- BG Sorter® CB Cross-Belt
- BG Pouch System
- BG Sorter® ET Tilt-Tray
-
Conveying Technology
- Conveying Technology
- Air-supported belt conveyor
- Apron Conveyors
- Bucket Elevators
- Components
- Conveyor Systems for Alternative Fuels (AFR)
- Drive Stations
- Feeding Hoppers
- Hopper Cars
- Mobile Conveyors
- Overland Belt Conveyors
- Pipe Conveyors
- Screw conveyor
- Shifting Heads
- Tripper Cars
- Troughed Belt Conveyors
- U-Shape Conveyors
- Opencast Mining Systems
- Stockyard Systems
- Mineral Processing
- Port Technology
- Loading Technology
- Filling Technology
- Palletising Technology
- Packaging Technology
- Customer Support
-