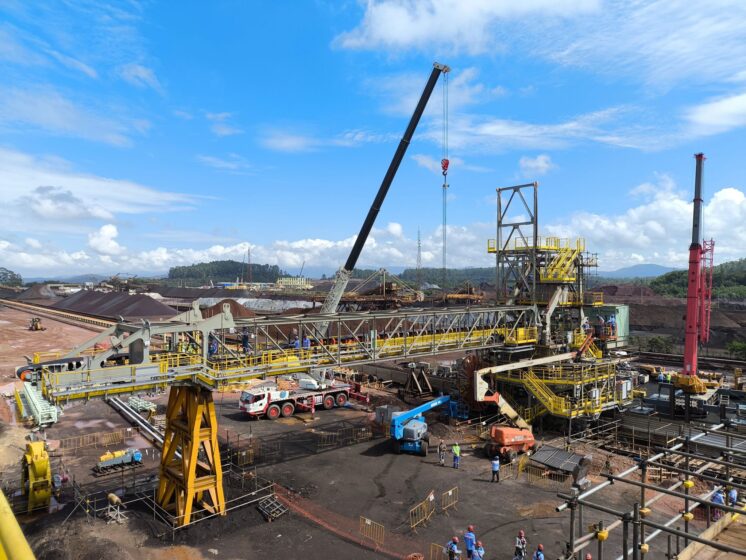
-
- Industrie-Lösungen
- Flughafen
- Baustoffe
- Zement / AFR
- Chemische Industrie
- Kurier, Express & Paket (KEP)
- E-Commerce
- Minerals & Mining
- Häfen & Terminals
- Kraftwerke
- Fashion
- Konsumgüter
- Einzelhandel
- Metallurgie
- Düngemittelindustrie
NACHHALTIGKEIT made differentUnser Engagement für nachhaltige EntwicklungAls unabhängiges Familienunternehmen fühlt sich die BEUMER Group den Prinzipien einer nachhaltigen Entwicklung verpflichtet. Durch starke Partnerschaften haben wir ein tiefes Verständnis für die Nachhaltigkeitsthemen unserer Schlüsselindustrien entwickelt und ermöglichen unseren Partnern, ihre Nachhaltigkeitsziele zu erreichen.Mehr erfahren -
- Produkte & Systeme
-
Gepäckförderanlagen
- Gepäckförderanlagen
- Airport Software Suite
- Automatisierter Container-Entlader
- BEUMER autover® unabhängiges Trägersystem
- Baggage Loader – Gepäcklader
- Baggage Manipulator
- Gepäckentlader für Flughäfen (Baggage Unloader)
- CrisBag® Gepäcktransportsystem auf Behälterbasis
- CrisBag® Self Bag Drop – Gepäckaufgabe
- CrisBelt Gepäckförder-System
- CrisCheck® Check-In Förderer
- CrisClaim® Gepäckausgabe-Karussells
- CrisStore® Rack-basiertes Lagersystem
- Kippschalen-Sortiersystem
-
Logistics Systems Technologie
- Logistics Systems Technologie
-
KEP Software Suite
- KEP Software Suite
- KEP -Artikelidentifizierung – Präzision und Effizienzsteigerung gewährleisten
- KEP – Steuerung des Materialflusses – Ermöglichen Sie durchgängig Effizienz
- KEP – Überwachung- Den vollständigen Überblick haben
- KEP- Tools für Wartung und Leistung – Die richtigen Hilfsmittel haben
- KEP – Business Intelligenz – Lernen und Planen durch Datenerfassung
- KEP – Training – Qualifiziertes und selbstbewusstes Personal schaffen
- Automatic Parcel Singulator
- BEUMER Kippstation
- BG Line Sorter
- BG Parcel Belt Conveyor – Paket Förderband
- BG Sorter® CB Cross-Belt
- BG Sorter® ET Tilt-Tray
- BG Pouch System
- Fördertechnik
- Tagebautechnik
- Lagerplatztechnik
- Aufbereitungstechnik
- Hafentechnik
- Verladetechnik
- Abfülltechnik
- Palettiertechnik
- Verpackungstechnik
- Customer Support